Industrial FTIR Spectrometer Systems For Chemical Manufacturing & Reaction Monitoring
The chemical process industries encompass many complex and sophisticated chemical and physical processes, reactions and unit operations.
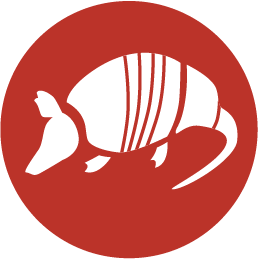
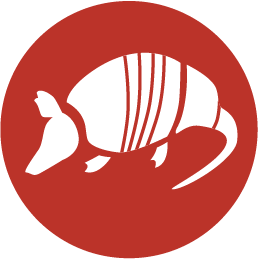
Testimonial
“We have been searching for a rugged industrial infrared ATR spectrometer. We have found the IRmadillo to be compact, robust and easy to implement on-line. The process installation is now finalized and we are collecting good results. The instrument is working like clockwork, demonstrating remarkable stability and precision on our application.”
Principal Scientist
International Agrochemical Company
The IRmadillo for Monitoring Chemical Manufacturing - Specialty, Bulk & Petrochemicals
The chemical process industries encompass many complex and sophisticated chemical and physical processes, reactions and unit operations. Processes may be batch or continuous, high volume or small throughput, commodity or specialized, but in every case there is a need for instrumentation to visualize, control and optimize the process and to improve efficiency and profitability. Basic instrumentation such as flow, temperature, pressure, level and pH sensors is an absolute necessity in this regard. While these instruments are inexpensive and easy to install, the information they provide is basic and does not directly measure the chemical composition of the process. With the advent of Industry 4.0, the bringing together of multiple sources of real-time information for deeper process understanding and optimization means that more advanced on-line analytical methods are called for.
Analytical experts are used to using high-performance equipment in laboratory settings, (such as NMR, HPLC and reaction control systems with integrated spectrometers), but these are simply not suitable for manufacturing environments. Moreover, many of these instruments are not stable enough to survive the long periods between turnarounds which are a typical feature of continuous processes. So how can the quality of laboratory instruments be taken out onto the plant?
The answer lies in industrial-grade spectrometers, providing real-time spectra that can be analyzed to provide concentration traces, batch modeling and descriptive statistics of a campaign. They can be installed on both batch and continuous processes, and work with a large range of different chemicals and process conditions. The most important feature of spectroscopy is not whether it can work or not, but in choosing the right technique for the process.
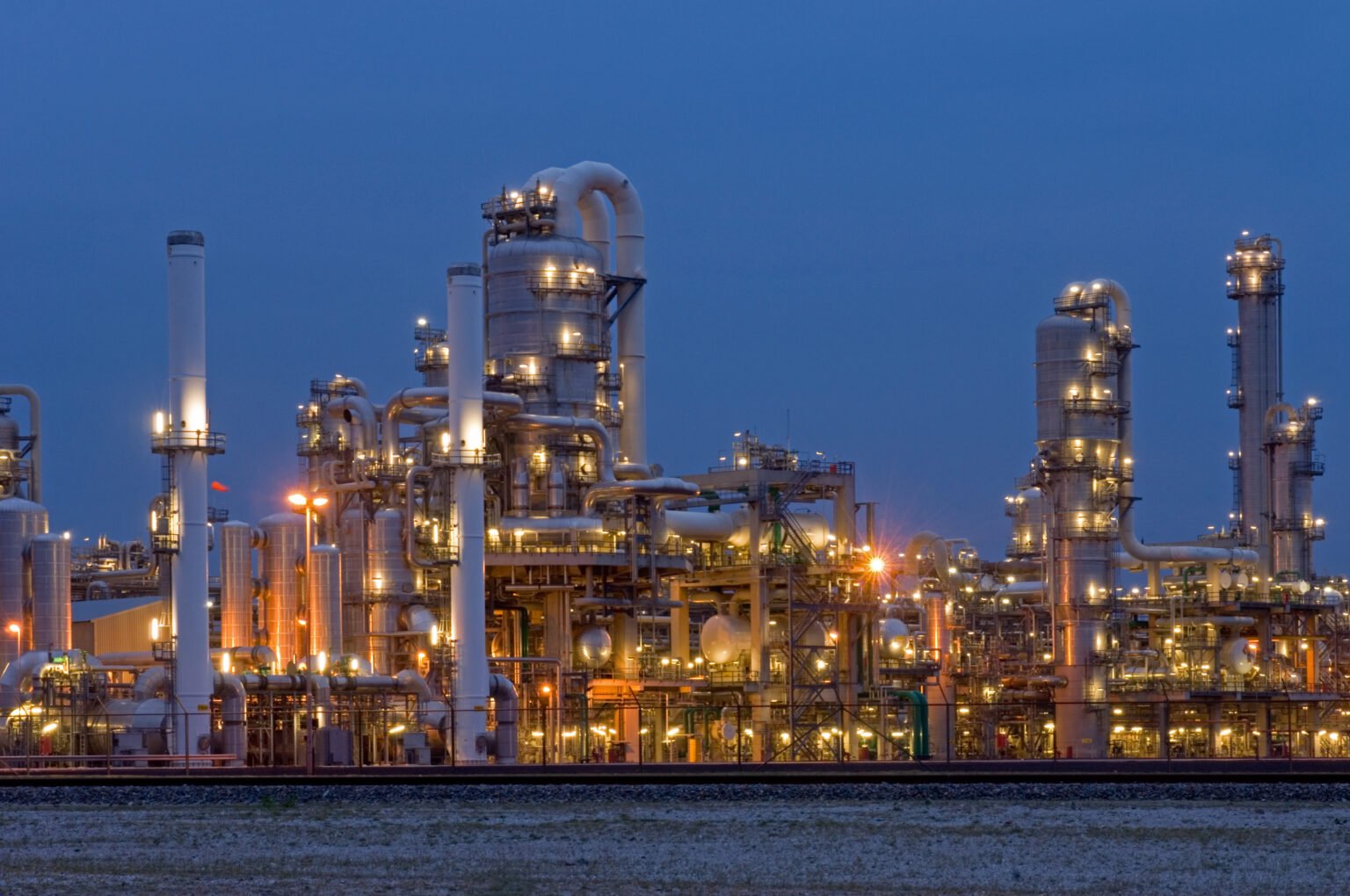
Using the IRmadillo to
Monitor Chemical Production
There are an almost unlimited number of different chemical reactions in use in the chemical industry, and the vast majority of those can be studied using FTIR. A representative list of processes that have strong features in the infrared spectrum are:
- Transition metal catalyzed coupling reactions (i.e. Cativa and Monsanto reactions)
- Addition, elimination and substitution chemical reactions
- Protection and deprotection steps
- Chemical rearrangements
- Hydrogenation and other catalyzed reactions
Unit operations such as crystallization, distillation, absorption and separation also commonly require on-line analytical information in order to be operated safely and efficiently.
Any process that has a change in the chemical functional groups present will have an infrared spectrum, and even slight changes in chemical (for example reduction of a carbonyl to an alcohol) will have a clear feature that can be used to track reaction progress. Additionally, FTIR can be used as a concentration meter in purification and separation processes, or even to be used as a quality control on reagent loading/unloading – for example, checking water levels in solvent before use to prevent dangerous side reactions from occurring with reactive reagents.
The IRmadillo can easily monitor the following unit operations:
- Distillation
- Crystallization
- Separation
- Purification
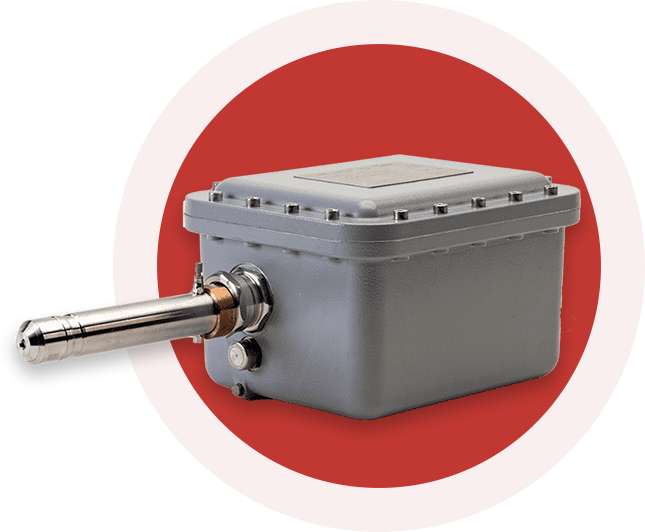
The benefits of on-line analysis compared to lab-based analysis
There are many different reasons why on-line analysis can be considered an improvement over off-line laboratory analysis. Here are three main benefits from using the IRmadillo compared to off-line sampling and analysis:
Safety: Some chemicals (for example, cyanides due to toxicity, or epoxides due to high reactivity and pyrophoric tendencies) cannot be handled safely. Taking samples off-line from pipelines or railcars is not practical or safe, and needs to be avoided as much as practical.
Short-lived chemicals: Some chemicals (for example free radicals or reactive intermediates) can be very short lived, and almost impossible to collect and bring to a laboratory for analysis. In this case only an on-line measurement allows detection and monitoring of the intermediates.
Real-time fine process control: Real-time process control can only be achieved with a real-time measurement. By the time a laboratory measurement has reported its result to the control room it is entirely possible that the process is completely different, and the result is no longer representative.
What about other instruments – Raman, near infrared (NIR), & refractive index monitors?
Raman spectroscopy is similar to the FTIR that drives the IRmadillo’s process monitoring, but it can be very strongly and negatively affected by particles and bubbles in the solution, as well as showing strong fluorescence in many cases.
Near infrared (NIR) technologies provide much less specific information than FTIR, however they can also be very cost-effective instruments. So even though they can give less specific and accurate results compared to an FTIR or Raman, they may be good enough for some situations.
Standard FTIR instruments contain delicately balanced optics that are highly susceptible to vibration, along with fragile fiber-optic cables making the use of standard FTIRs directly in manufacturing conditions a real challenge.
Refractometers are cost-effective measurements for simple mixtures with very good process control already. Refractometers work very well measuring one component in another component, but cannot cope with complicated mixtures or a change in temperature (any temperature variation over ± 2°C can cause measurement problems for refractometers).
The IRmadillo for
Chemical Production
The IRmadillo was designed for ease of use, so in many cases does not require any sample conditioning or specific handling. The section above specifies the operating conditions of the various models. If you process lies outside of these (for example, a high temperature alkali process) then some sample conditioning may be required – Keit will work with you to establish a solution.
The IRmadillo was originally developed for the petrochemicals and oil and gas industries – so it can take a beating. It has an ambient temperature range of -20 °C to 55 °C so temperature variations aren’t a problem. It also has an IP65 rating meaning it doesn’t mind whatever the weather throws at it.
Fouling is a problem for ATR based probes, but the calibration Keit builds for measurement will identify when this sort of problem occurs. Calibrations can also be built to include small amounts of scale or fouling to make them more robust until you have a time to clean the probe.
Explore our
Application Library
There’s more to find out. Feel free to download and read our application notes and
brochure by browsing our application library.
The IRmadillo for
Monitoring Chemical Processes
If you purchase the IRmadillo for chemical manufacturing you will receive:
- IRmadillo process analyzer
- Interface and mounting accessories to integrate with your process (following a consultation with your engineering team)
- IRmadillo controller
- Calibration services
- Ongoing technical and recalibration support (as per your warranty or maintenance contract)
Contact Us
Download
IRmadillo Brochure
Keit enables better control of industrial processes by providing real-time chemical reaction analysis of liquids. The IRmadillo mid-infrared spectrometer has practical applications across multiple industries.